New Facility Code Challenges at NASSCO Shipyards
General Dynamics NASSCO, designer and ship builder for the U.S. Navy, required an upgrade of their steelblasting and paint facility at their shipyard location in San Diego, California. During the planning and building phase Klausbruckner & Associates was contracted to provide expert fire and building code services on Navy’s largest new construction shipyard on the West Coast.
General Dynamics NASSCO has been designing and building ships since 1959 focusing on the design and development of auxiliary and support ships for the U.S. Navy and oil tankers and dry cargo carriers for commercial markets. NASSCO employs more than 4,600 people and is the only major ship construction yard on the West Coast of the United States. As part of the continued upgrade and modernization of the shipyard, a new spray application and steel blasting building needed to be added to the existing facilities. Klausbruckner & Associates was asked to review the proposed building to ensure design and code compliance.
The Project & Challenges
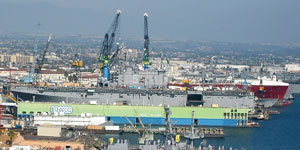
National Steel and Shipbuilding Company (NASSCO)
One of the major challenges in this project was the sheer size of the spray booths and steel blasting facilities and all the related challenges that come along with spray applications of this magnitude. To put this into perspective, the building had a size of approximately 70,000 sq ft, with 40,000 sq ft used exclusively for spray applications, subdivided into 6 large spray booths, and 30,000 sq ft reserved for “steel blasting” operations.
The architecture of the building was designed to allow large parts of ships i.e., entire ship hull sections of aircraft carriers, to be rolled into one of six large-scale spray booth cells. The steel blasting section, as it is common in the shipbuilding and ship repair industry, was designed for abrasive blasting for surface preparation to remove old paint and other surface materials, such as rust, mill scale, dirt, and salts.
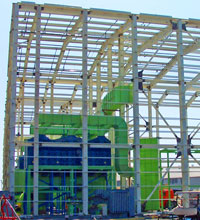
Custom Designed Dust Collector
Based on the large scale of the operation, a particular challenge was the specification and integration of the industrial ventilation and filtration systems, which involves the use of supply and exhaust ventilation to control emissions, exposures, and chemical hazards in the facility. For surface preparation and spraying of the enormous sized hull sections up to six operators needed at any point in time to be able to spray the hull sections. This meant that the evaporation of thin layers of flammable liquids on large surfaces resulted in a large amount of flammable vapors in the air. To be more specific, the LFL (Lower Flammable Limit), which measures the optimal range for ignition or deflagration range (critical ratio of air to fuel in the air) is directly affected by not only the amount of fuel, but also the evaporation rate as a result of spread of fuel on large surface areas.
This required the ventilation and filtration system to be carefully specified in order to be able to handle these large amounts of flammable vapors and also to reduce the risk of fire or explosion within the dust collector and ductwork. In compliance with the California Mechanical Code, a Class 4 duct system to handle highly abrasive particles in high concentrations needed to be integrated in the steel blasting areas to maintain proper airflow in combination with the large custom-designed industrial dust collection systems.
The building design and its provisions to ensure fire safety needed to be reviewed and revised. The entire building was prefabricated and shipped to location. However, when this prefabricated building was built, it was not apparent that the regulations at the location it was designed and built were different from the requirements at the building location and at the time of installation. To provide an example, while LFL (Lower Flammable Limit) sensors were installed in the building, sprinklers were not included in the design or planned into the building protection systems.
Results
A comprehensive solution approach was taken to successfully address all fire and building code related issues of the proposed spray and steel blasting operations. A code compliance assessment along with negotiated alternative means and methods were used to solve many of the mentioned challenges faced by the construction team. On the other hand achieving complete and total code compliance is difficult for these types of facilities. For example, spill control and secondary containment was a condition of approval for this building. However it could not be achieved for the building, because large heavy ship parts could not be transported into the building, if curbs or sills were used. The pre-fabricated metal building, along with the heavy parts, also did not allow for recessed floors. Drainage system would require sloped floors, which would result in uneven application of the paint. Since the entire NASSCO site was equipped with spill control and secondary containment, the fire department accepted the site spill control as an alternative means and methods, as well as due to practical difficulty, to that required for the building.
Summary
The Klausbruckner & Associates team is proud to have provided engineering leadership for this new steelblasting and paint facility at General Dynamics NASSCO. Our team of experts along with the construction and design team worked with the Building and Fire Department of the City of San Diego to gain acceptance for alternative methods of compliance and to meet and to address all the challenges associated with this unique facility.
The result of these engineering efforts will lead to increased environmental safety and operational efficiency of the NASSCO Steelblasting and Paint Facility. We thank General Dynamics NASSCO and the design and construction team for making Klausbruckner & Associates Inc. a part of this unique project.